Cases de sucesso
Cases de sucesso

Conjunto completo!
O que o cliente diz?
Neste projeto em Canoinhas, o cliente buscava solucionar questões logísticas na fábrica de papel. Antes da automação, a produção era movida manualmente com paletes e empilhadeiras, envolvendo muitos funcionários e altos custos logísticos, além de preocupações com segurança devido às empilhadeiras circulando entre os funcionários.
A solução envolveu a criação de um layout aéreo, com esteiras transportadoras direcionando a produção para elevadores contínuos a cinco metros de altura, eliminando obstáculos no piso da fábrica.
Foram instalados também pórticos e suportes para sustentar as esteiras, resultando em uma obra limpa. Além disso, um novo elevador de carga de dez toneladas foi construído para carregar bobinas jumbo de papel e demais produtos.
A automação foi renovada com aplicação de etiquetas e leitores de QR Code, permitindo a separação automática dos produtos para a paletização. O cliente recebeu painéis de comando com IHM’s para ajustar e monitorar toda a linha, tornando-a flexível para diferentes formatos de produtos e demandas.
Um elevador foi instalado para facilitar o deslocamento entre os prédios, eliminando a necessidade de subir escadas em um desnível de quase dez metros.
Todos os equipamentos foram projetados para operar em três turnos, 24 horas por dia, 7 dias por semana, e seguiram as normas de segurança da NR-12 para sua construção.
O projeto foi destacado pela abordagem aérea, automação eficiente e atenção à segurança, atendendo aos requisitos de qualidade e segurança do mercado.
Diferenciais:
A implementação de um layout aéreo trouxe uma abordagem inovadora para a movimentação de produtos na fábrica. Ao elevar as esteiras transportadoras e os elevadores contínuos a cinco metros de altura, eliminaram-se os obstáculos no piso da fábrica, otimizando o fluxo de produção e liberando espaço valioso no chão da fábrica para outras atividades.
A introdução de etiquetas e leitores de QR Code permitiu a automação eficiente do processo de separação e paletização dos produtos. Isso reduziu a necessidade de intervenção manual, aumentou a velocidade de processamento e minimizou erros, resultando em uma operação mais eficiente e precisa.
O projeto foi concebido com foco na segurança dos funcionários e dos equipamentos. Todos os elementos, desde as estruturas aéreas até os equipamentos de automação, foram projetados e instalados em conformidade com as normas de segurança da NR-12. Além disso, a eliminação da circulação de empilhadeiras entre os funcionários reduziu significativamente os riscos de acidentes.
A linha de produção foi projetada para ser altamente flexível, capaz de lidar com diferentes formatos de produtos e demandas variáveis. Os painéis de comando com IHM’s permitiram ajustes rápidos e fáceis na linha de produção, garantindo que a fábrica pudesse adaptar-se facilmente a mudanças nas necessidades do mercado sem comprometer a eficiência ou a qualidade.
O elevador de carga de Canoinhas apresentou diferenciais notáveis, destacando-se pela capacidade de transporte de até dez toneladas, dimensões generosas da cabine, integração ao sistema automatizado da fábrica e conformidade com normativas de segurança. Sua versatilidade e eficiência otimizaram a movimentação de grandes bobinas de papel entre diferentes níveis da instalação, contribuindo significativamente para a melhoria da logística e da eficiência operacional na fábrica de papel.
Resultado
O resultado do projeto em Canoinhas foi altamente positivo. A implementação das soluções logísticas, como o sistema de esteiras aéreas, elevadores de carga e automação eficiente, resultou em uma significativa otimização dos processos de produção e logística na fábrica de papel. Isso se traduziu em uma redução substancial nos custos operacionais, uma maior eficiência na movimentação de materiais, um ambiente de trabalho mais seguro e uma maior capacidade de resposta às demandas do mercado. O projeto atendeu com sucesso aos requisitos de qualidade, segurança e eficiência do cliente, proporcionando benefícios tangíveis em termos de produtividade e competitividade.

Solução completa, conjunto de esteiras, elevadores de carga e contínuo!
Neste projeto em Canoinhas, o cliente buscava solucionar questões logísticas na fábrica de papel. Antes da automação, a produção era movida manualmente com paletes e empilhadeiras, envolvendo muitos funcionários e altos custos logísticos, além de preocupações com segurança devido às empilhadeiras circulando entre os funcionários.
A solução envolveu a criação de um layout aéreo, com esteiras transportadoras direcionando a produção para elevadores contínuos a cinco metros de altura, eliminando obstáculos no piso da fábrica.
Foram instalados também pórticos e suportes para sustentar as esteiras, resultando em uma obra limpa. Além disso, um novo elevador de carga de dez toneladas foi construído para carregar bobinas jumbo de papel e demais produtos.
A automação foi renovada com aplicação de etiquetas e leitores de QR Code, permitindo a separação automática dos produtos para a paletização. O cliente recebeu painéis de comando com IHM’s para ajustar e monitorar toda a linha, tornando-a flexível para diferentes formatos de produtos e demandas.
Um elevador foi instalado para facilitar o deslocamento entre os prédios, eliminando a necessidade de subir escadas em um desnível de quase dez metros.
Todos os equipamentos foram projetados para operar em três turnos, 24 horas por dia, 7 dias por semana, e seguiram as normas de segurança da NR-12 em sua construção.
O projeto foi destacado pela abordagem aérea, automação eficiente e atenção à segurança, atendendo aos requisitos de qualidade do mercado.
Resultado
O resultado do projeto em Canoinhas foi altamente positivo. A implementação das soluções logísticas, como o sistema de esteiras aéreas, elevadores de carga e automação eficiente, resultou em uma significativa otimização dos processos de produção e logística na fábrica de papel. Isso se traduziu em uma redução substancial nos custos operacionais, uma maior eficiência na movimentação de materiais, um ambiente de trabalho mais seguro e uma maior capacidade de resposta às demandas do mercado. O projeto atendeu com sucesso aos requisitos de qualidade, segurança e eficiência do cliente, proporcionando benefícios tangíveis em termos de produtividade e competitividade.
O que o cliente diz?
Diferenciais:
A implementação de um layout aéreo trouxe uma abordagem inovadora para a movimentação de produtos na fábrica. Ao elevar as esteiras transportadoras e os elevadores contínuos a cinco metros de altura, eliminaram-se os obstáculos no piso da fábrica, otimizando o fluxo de produção e liberando espaço valioso no chão da fábrica para outras atividades.
A introdução de etiquetas e leitores de QR Code permitiu a automação eficiente do processo de separação e paletização dos produtos. Isso reduziu a necessidade de intervenção manual, aumentou a velocidade de processamento e minimizou erros, resultando em uma operação mais eficiente e precisa.
O projeto foi concebido com foco na segurança dos funcionários e dos equipamentos. Todos os elementos, desde as estruturas aéreas até os equipamentos de automação, foram projetados e instalados em conformidade com as normas de segurança da NR-12. Além disso, a eliminação da circulação de empilhadeiras entre os funcionários reduziu significativamente os riscos de acidentes.
A linha de produção foi projetada para ser altamente flexível, capaz de lidar com diferentes formatos de produtos e demandas variáveis. Os painéis de comando com IHM’s permitiram ajustes rápidos e fáceis na linha de produção, garantindo que a fábrica pudesse adaptar-se facilmente a mudanças nas necessidades do mercado sem comprometer a eficiência ou a qualidade.
O elevador de carga de Canoinhas apresentou diferenciais notáveis, destacando-se pela capacidade de transporte de até dez toneladas, dimensões generosas da cabine, integração ao sistema automatizado da fábrica e conformidade com normativas de segurança. Sua versatilidade e eficiência otimizaram a movimentação de grandes bobinas de papel entre diferentes níveis da instalação, contribuindo significativamente para a melhoria da logística e da eficiência operacional na fábrica de papel.
Desafio:
O Instituto de Pesquisas Tecnológicas (IPT) solicitou o desenvolvimento de uma solução inovadora para tratar solos contaminados de forma eficiente, enquanto mantinha a mobilidade da unidade de tratamento. O desafio era criar um sistema capaz de realizar a injeção controlada de nano partículas de polímero em solos contaminados, seguindo os processos definidos pelos pesquisadores do IPT.
Solução Proposta:
Nossa equipe de engenharia se propôs a desenvolver um sistema completo, desde o equipamento para a injeção das nano partículas até a unidade móvel para deslocamento no local de tratamento. A solução foi projetada para ser altamente eficiente, com controles automatizados e um design que permite fácil mobilidade.
Desenvolvimento:
Criamos um equipamento especializado para a injeção controlada de nano partículas de polímero no solo contaminado. Este equipamento foi projetado para garantir precisão e uniformidade na distribuição das nano partículas, maximizando a eficácia do tratamento. Desenvolvemos uma unidade móvel de tratamento de solo, equipada com todos os componentes necessários para realizar o tratamento em campo.
Diferenciais:
A unidade móvel permite o tratamento de solos contaminados em diferentes locais, aumentando a eficiência e reduzindo os custos de transporte.
O equipamento desenvolvido garante a injeção controlada e precisa das nano partículas de polímero, garantindo um tratamento eficaz do solo contaminado.
Essa esteira foi fabricada seguindo os padrões FDA.
O sistema automatizado de preparação do composto e os controles via IHM permitem uma operação mais eficiente e precisa, reduzindo erros e aumentando a produtividade.c
O uso de nano partículas de polímero para o tratamento de solos contaminados é uma alternativa mais sustentável em comparação com métodos tradicionais, reduzindo o impacto ambiental.
Resultado:
A solução desenvolvida atendeu plenamente aos requisitos do IPT, proporcionando uma forma eficiente e móvel de tratar solos contaminados. Com controles automatizados, precisão na injeção de nano partículas e mobilidade aumentada, nossa solução é uma contribuição significativa para a preservação do meio ambiente e a saúde pública.
Desafio:
O Instituto de Pesquisas Tecnológicas (IPT) solicitou o desenvolvimento de uma solução inovadora para tratar solos contaminados de forma eficiente, enquanto mantinha a mobilidade da unidade de tratamento. O desafio era criar um sistema capaz de realizar a injeção controlada de nano partículas de polímero em solos contaminados, seguindo os processos definidos pelos pesquisadores do IPT.
Solução Proposta:
Nossa equipe de engenharia se propôs a desenvolver um sistema completo, desde o equipamento para a injeção das nano partículas até a unidade móvel para deslocamento no local de tratamento. A solução foi projetada para ser altamente eficiente, com controles automatizados e um design que permite fácil mobilidade.
Desenvolvimento:
Criamos um equipamento especializado para a injeção controlada de nano partículas de polímero no solo contaminado. Este equipamento foi projetado para garantir precisão e uniformidade na distribuição das nano partículas, maximizando a eficácia do tratamento. Desenvolvemos uma unidade móvel de tratamento de solo, equipada com todos os componentes necessários para realizar o tratamento em campo.
Diferenciais:
A unidade móvel permite o tratamento de solos contaminados em diferentes locais, aumentando a eficiência e reduzindo os custos de transporte.
O equipamento desenvolvido garante a injeção controlada e precisa das nano partículas de polímero, garantindo um tratamento eficaz do solo contaminado.
Essa esteira foi fabricada seguindo os padrões FDA.
O sistema automatizado de preparação do composto e os controles via IHM permitem uma operação mais eficiente e precisa, reduzindo erros e aumentando a produtividade.c
O uso de nano partículas de polímero para o tratamento de solos contaminados é uma alternativa mais sustentável em comparação com métodos tradicionais, reduzindo o impacto ambiental.
Resultado:
A solução desenvolvida atendeu plenamente aos requisitos do IPT, proporcionando uma forma eficiente e móvel de tratar solos contaminados. Com controles automatizados, precisão na injeção de nano partículas e mobilidade aumentada, nossa solução é uma contribuição significativa para a preservação do meio ambiente e a saúde pública.
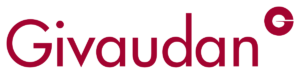
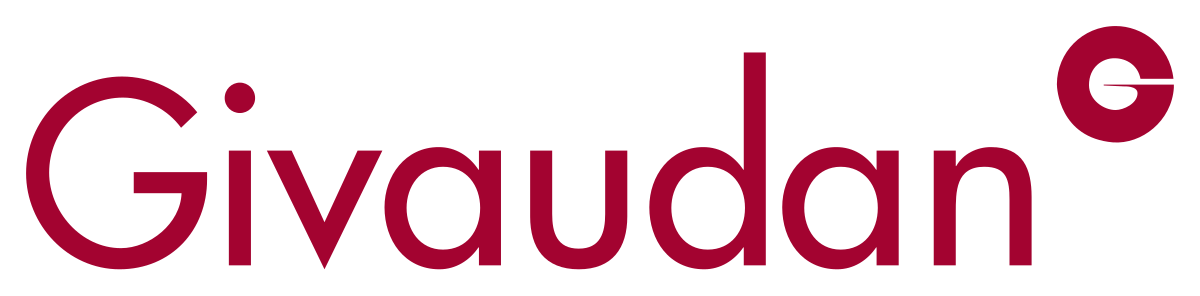
Esteiras de Rolete MAP
Desafio:
A Givaudan, líder global em fragrâncias e aromas, buscava modernizar sua linha de produção para atender aos mais altos padrões de segurança e higiene da indústria alimentícia. O desafio envolvia a implementação de uma solução que fosse totalmente em aço inoxidável, lavável, ergonomicamente adequada e capaz de atender aos requisitos da FDA. Além disso, era necessário integrar sistemas de detecção de metais e balança para garantir a qualidade dos produtos.
Diferenciais:
O projeto 100% em inox é especialmente adequado para ambientes que exigem alta higiene e resistência à corrosão.
A escolha do aço inoxidável (inox) para a fabricação desta esteira garante durabilidade, resistência à oxidação e facilidade de limpeza, além de manter a integridade dos produtos transportados, sem contaminá-los.
A integração de uma balança de precisão nesta esteira de roletes MAP traz diversos benefícios, incluindo controle preciso do peso dos produtos, redução de desperdícios, garantia de qualidade consistente, facilidade de verificação automatizada, melhoria na rastreabilidade e integração com sistemas de automação existentes.
Essa esteira foi fabricada seguindo os padrões FDA.
O FDA pode avaliar a conformidade da esteira de roletes MAP com regulamentos específicos relacionados à segurança alimentar, embalagem e processamento de alimentos. Isso inclui garantir que a esteira e seus componentes sejam fabricados com materiais seguros e adequados para uso em contato com alimentos.
O liftgate é o componente que foi adicionado à esteira de roletes para facilitar o carregamento e descarregamento de cargas. Ele consiste em uma seção da esteira que pode ser elevada ou abaixada conforme necessário. Isso permite que caixas, paletes ou outros itens sejam facilmente transferidos da esteira para outra superfície ou vice-versa, sem a necessidade de levantamento manual ou o uso de equipamentos adicionais.
Essas esteiras são projetadas para suportar procedimentos de limpeza rigorosos, incluindo lavagem com água e produtos de limpeza desinfetantes, garantindo a remoção de quaisquer resíduos, sujeira ou contaminantes que possam acumular durante o processo de produção.
A esteira de roletes MAP ergonômica é projetada para garantir conforto e segurança aos operadores. Com altura ajustável, sistemas de amortecimento e controles de fácil acesso, reduz o risco de lesões, promovendo a eficiência e bem-estar físico. Simplifica a manutenção e limpeza, aumentando a produtividade. Prioriza a saúde dos trabalhadores, melhorando a eficiência operacional e criando um ambiente de trabalho mais seguro e saudável.
A integração do detector de metais com sistemas de controle de qualidade existentes na linha de produção permite uma inspeção contínua e automatizada dos produtos. Além de garantir a segurança do produto, o detector de metais protege a reputação da marca ao demonstrar um compromisso com a qualidade e segurança dos produtos. Ele também contribui para a redução de riscos à saúde dos consumidores.
Resultado
A nova linha de produção da Givaudan atendeu plenamente às expectativas, proporcionando um ambiente de trabalho seguro, higiênico e eficiente. A implementação das esteiras de roletes MAP melhorou significativamente a qualidade e a rastreabilidade dos produtos, enquanto a ergonomia integrada aumentou a produtividade e o conforto dos operadores. A solução customizada permitiu à Givaudan manter sua reputação de excelência na indústria alimentícia, destacando-se pela inovação e compromisso com a qualidade.
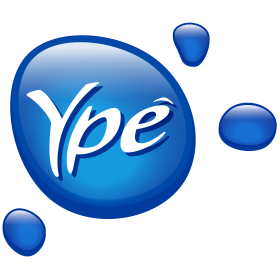
Elevador 22m
Objetivo do Cliente:
A YPE, uma empresa líder no setor industrial, buscava um equipamento robusto e eficiente para otimizar seus processos de produção. Com um foco em aumentar a eficiência e a segurança em suas operações, eles procuravam uma solução que atendesse às suas necessidades específicas, incluindo requisitos de espaço físico, altura e projeto especial.
Desafio MRSUL:
O principal desafio era o espaço físico limitado para instalação do equipamento. Além disso, a altura do elevador que chegaria a mais de 20m, e a complexidade do projeto eram desafios adicionais. Vale lembra que devido a limitação de espaço a casa de máquina seria que ser instalada lateralmente, visto que a parte superior estaria comprometida com uma ponte rolante.
Soluções Apresentadas:
Para enfrentar os desafios apresentados pela YPE, a Mrsul desenvolveu um equipamento sob medida, capaz de atender às especificações exigentes do cliente. A solução proposta incluiu:
O equipamento foi projetado com um design compacto para otimizar o espaço físico disponível. A casa de máquinas foi instalada na lateral do elevador, atendendo à limitação de altura sem comprometer a capacidade de carga de 2 toneladas.
Para facilitar o acesso aos pavimentos, foram instaladas portas de abertura vertical automáticas. No térreo com sentido de porta 0/180º. Essas portas garantem uma operação suave e segura, proporcionando maior conveniência e segurança para os operadores e funcionários da YPE.
O equipamento foi projetado com cancelas dentro da cabine para evitar a obstrução das barreiras infravermelho. Além disso, foi implementada a NR-12, garantindo padrões elevados de segurança operacional.
O painel de comando industrial foi posicionado em altura ergonômica para fácil acesso durante a manutenção, proporcionando maior eficiência e praticidade aos técnicos responsáveis.
Devido ao espaço limitado, o equipamento foi entregue em módulos e montado em tempo recorde, em apenas 4 dias. Isso minimizou o tempo de inatividade da YPE e permitiu que suas operações voltassem ao normal o mais rápido possível.
O elevador foi construído para alcançar os 22 metros de altura necessários, com capacidade para atender aos 5 pavimentos conforme o projeto especial da YPE. O último pavimento foi especialmente adaptado para acomodar a passagem da ponte rolante, garantindo a integração perfeita do equipamento com as operações existentes da empresa.
A decisão de posicionar a casa de máquinas na lateral do elevador não apenas resolveu o desafio específico de altura enfrentado pela YPE, mas também proporcionou uma otimização significativa do espaço disponível no ambiente industrial. Além disso, essa abordagem permitiu um acesso facilitado para manutenção e inspeção, garantindo uma operação contínua e confiável do equipamento.
Resultado:
Com a solução desenvolvida, a YPE conseguiu atingir seus objetivos de aumentar a eficiência e a segurança em suas operações industriais. O equipamento robusto e customizado proporcionou uma integração perfeita aos processos existentes da empresa, garantindo uma produção mais eficiente e confiável. Além disso a manutenção preventiva é feita regulamente garantindo a eficiência do equipamento, e mostra o cuidado que a YPE possui com seu produto.
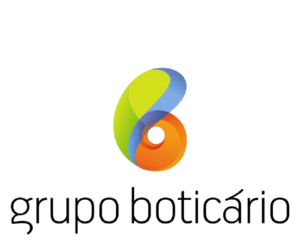
2 Elevadores ao mesmo tempo
Objetivo do cliente:
O Boticário, renomada empresa de cosméticos com sede em São José dos Pinhais, Curitiba, enfrentava constantes problemas com os elevadores de carga em sua unidade fabril. Os equipamentos antigos frequentemente quebravam, impactando negativamente na eficiência operacional da fábrica. O cliente buscava uma solução que resolvesse esses problemas de forma rápida e eficaz, garantindo a continuidade das operações durante o processo de substituição dos elevadores. Além de Restrições de acesso e prazo de entrega, não poderia ter poço para instalação do equipamento o acesso seria por fora do prédio com guindaste de 100 Toneladas e teríamos apenas 04 dias para Desmontagem do Elevador antigo e montagem do novo
Soluções apresentadas:
A MRSUL apresentou uma solução abrangente e inovadora para atender às necessidades específicas de O Boticário em relação à substituição dos elevadores de carga. Diante das restrições de acesso ao prédio e do curto prazo de entrega de apenas quatro dias, desenvolvemos um plano de ação detalhado para garantir o sucesso do projeto. Aqui está uma visão detalhada da solução proposta:
A MRSUL não apenas forneceu uma solução padrão, mas adaptou-se às necessidades específicas do cliente. Reconhecendo as restrições de acesso e o curto prazo de entrega, nossa equipe desenvolveu uma estratégia sob medida para garantir uma transição suave e eficiente para os novos elevadores.
A MRSUL assumiu a responsabilidade de gerenciar todas as fases do projeto, desde o planejamento inicial até a entrega final. Nossa abordagem orientada para resultados garantiu que todas as tarefas fossem concluídas dentro do prazo estabelecido, mantendo a comunicação transparente com o cliente em cada etapa do processo.
Para superar as restrições de acesso ao prédio, empregamos tecnologia de ponta, incluindo guindastes de alta capacidade e equipamentos de içamento especializados. Isso permitiu a remoção dos elevadores antigos e a instalação dos novos módulos de forma eficiente e segura, minimizando o tempo de inatividade da fábrica.
Em cada fase do projeto, a MRSUL priorizou a qualidade e segurança. Desde a avaliação inicial até a conclusão da instalação, aderimos aos mais altos padrões da indústria para garantir a durabilidade e confiabilidade dos novos elevadores de carga.
Resultado:
A MRSUL concluiu com sucesso a modernização do sistema de elevadores de carga para O Boticário dentro do prazo estabelecido de quatro dias. Apesar dos desafios relacionados ao acesso restrito e à ausência de poço para instalação, os novos elevadores foram montados com precisão e segurança. O cliente ficou extremamente satisfeito com o resultado, pois agora dispõe de equipamentos modernos e confiáveis que contribuirão para a otimização de suas operações fabris. A parceria entre O Boticário e a MRSUL demonstrou mais uma vez a excelência em soluções de elevação e logística, consolidando a reputação da empresa como líder no mercado.
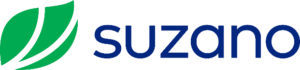
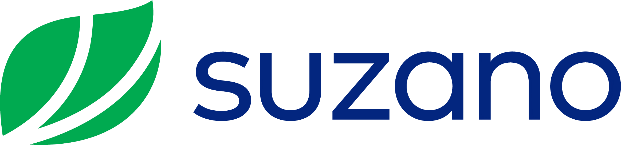
Substituição de taliscas transportadoras.
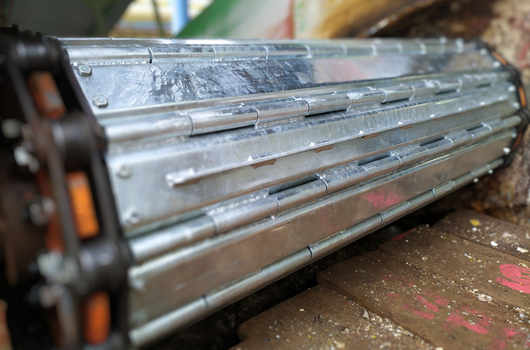
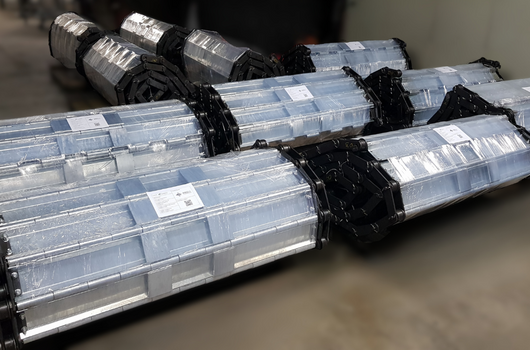
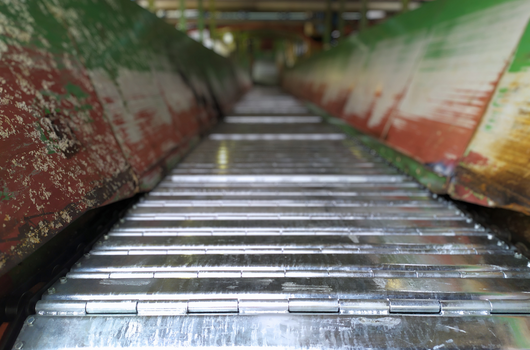
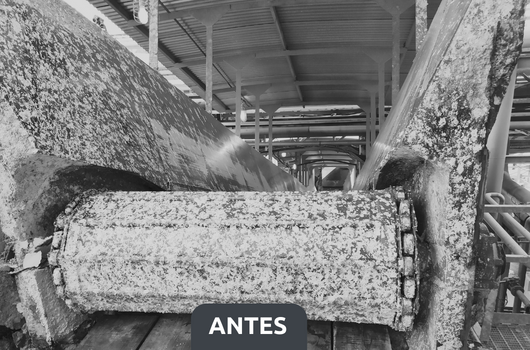
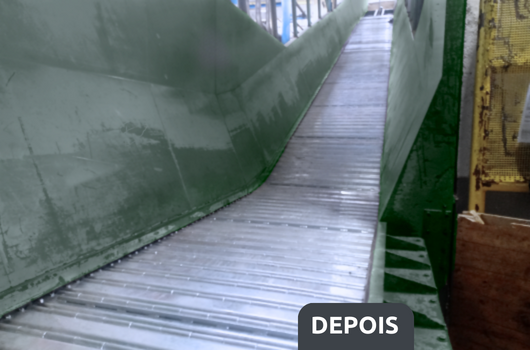
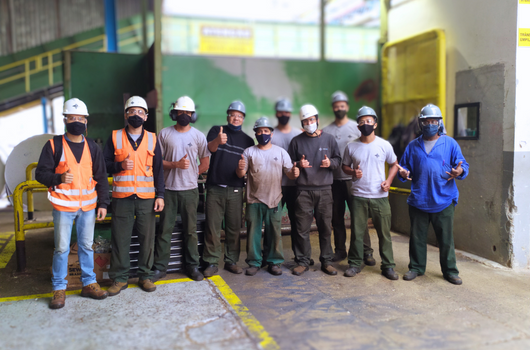
Objetivo:
Restaurar o transportador de talisca para suportar alta demanda. O cliente, Suzano, enfrentava constantes problemas com o transportador de celulose, onde as taliscas quebravam durante o carregamento por empilhadeiras, comprometendo a eficiência do processo.
Desafios:
- Taliscas quebravam constantemente durante o carregamento, ficavam fragilizadas e amassadas devido ao trabalho de alto impacto.
- Necessidade de aumentar a resistência e durabilidade das taliscas para suportar a capacidade necessária.
- Corrosão das taliscas devido ao ambiente industrial, reduzindo sua vida útil e aumentando custos de manutenção.
- Substituição necessária da corrente de tração, rodas dentadas e reparos na parte estrutural para garantir alta performance do transportador.
Soluções apresentadas:
Foi desenvolvido um projeto sob medida e inovador para as taliscas, levando em consideração as especificidades do transporte de celulose e a necessidade de suportar o carregamento por empilhadeiras. As taliscas foram dimensionadas para suportar a capacidade necessária e resistir ao alto impacto gerado durante o carregamento, garantindo sua durabilidade e eficácia no processo.
Todas as taliscas foram submetidas a um processo de galvanização a fogo, que consiste na aplicação de uma camada de zinco sobre o metal. Esse processo cria uma barreira resistente contra a corrosão, protegendo as taliscas do ambiente industrial e aumentando significativamente sua vida útil.
A galvanização a fogo contribuiu para a redução dos custos de manutenção, uma vez que as taliscas não precisarão ser substituídas com tanta frequência devido à corrosão.
Foi realizada a substituição da corrente de tração e das rodas dentadas, componentes essenciais para o funcionamento eficiente do transportador. Além disso, foram feitos reparos na parte estrutural do transportador, garantindo sua integridade e eficácia operacional.
Essas medidas foram fundamentais para garantir a alta performance do transportador, evitando falhas mecânicas que poderiam comprometer a produção.
O painel
Todos os materiais utilizados na restauração do transportador foram de alta qualidade e provenientes de fornecedores confiáveis. A escolha de materiais industriais de primeira linha assegurou a qualidade e eficácia do transportador, garantindo sua durabilidade e resistência às condições de operação adversas.
de comando industrial foi posicionado em altura ergonômica para fácil acesso durante a manutenção, proporcionando maior eficiência e praticidade aos técnicos responsáveis.
A atividade de restauração foi planejada e executada de forma eficiente, visando minimizar os impactos na produção da Suzano.
O trabalho foi realizado em um prazo de 6 dias, operando 24 horas por dia, demonstrando comprometimento com o cliente e agilidade na resolução dos problemas identificados no transportador.
Essa rápida execução contribuiu para a redução do tempo de paralisação do equipamento e para a retomada ágil das operações de transporte de celulose.
Resultados:
A intervenção para restauração do transportador de talisca da Suzano foi um sucesso, resultando em uma série de benefícios significativos. Os problemas recorrentes de quebra, fragilização e amassamento das taliscas durante o carregamento foram completamente eliminados, proporcionando uma operação mais suave e eficiente. Além disso, a galvanização a fogo das taliscas estendeu consideravelmente sua vida útil, reduzindo os custos de manutenção associados à substituição frequente. Com a substituição da corrente de tração, rodas dentadas e realização de reparos estruturais, a performance do transportador foi otimizada, resultando em uma operação mais eficiente e confiável. A execução do trabalho com capricho, precisão e dentro do prazo estabelecido levou à satisfação do cliente Suzano, consolidando a confiança na capacidade da empresa em fornecer soluções eficazes e de alta qualidade. Em resumo, a restauração do transportador não apenas resolveu os problemas existentes, mas também proporcionou melhorias significativas em termos de durabilidade, desempenho e satisfação do cliente.
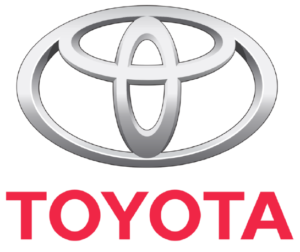
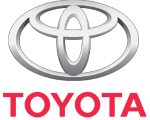
Esteiras de roletes
Objetivo do cliente:
Objetivo do Cliente: A Toyota, conhecida por sua exigência e rigor na qualidade de seus processos, buscava uma solução eficiente para a linha de montagem do Toyota Corolla. O objetivo era desenvolver uma esteira de alta capacidade capaz de movimentar os motores dos carros em um circuito específico, permitindo que cada componente fosse montado em segundos, atendendo à demanda rápida da produção.
Desafios:
- Criar uma esteira robusta que suportasse cargas superiores, pois a interroll não fabrica roletes com a capacidade necessária para o projeto.
- Garantir uma movimentação extremamente rápida dos motores para manter o tempo de montagem de cada componente.
- Assegurar que qualquer problema mecânico não parasse a linha de produção, mantendo assim a eficiência operacional.
Soluções apresentadas:
- Desenvolvimento de uma esteira personalizada, projetada desde os mínimos detalhes até os roletes, para atender às especificações da Toyota.
- Capacidade de suportar cargas superiores, garantindo a movimentação rápida dos motores ao longo do circuito de montagem.
- Cada ponto ao longo da esteira determinava uma etapa de montagem, permitindo o fluxo contínuo do processo.
- Desenvolvimento de um sistema de segurança chamado indexador para evitar paradas na linha de produção em caso de problemas mecânicos. Permitia que os operadores, em caso de falha, pudessem manualmente liberar o módulo redutor e empurrar os motores com total segurança, enquanto a equipe de manutenção realizava os reparos necessários.
- Garantia de eficiência operacional contínua, minimizando interrupções na produção.
Foi implementado um transportador laranja móvel, equipado com um atuador pneumático, para receber os motores dos robôs, transportá-los para as células de montagem e, em seguida, movê-los para a parte inferior do carro, onde seriam instalados. Essa solução permitiu uma montagem eficiente e rápida dos motores, contribuindo para a qualidade e produtividade da linha de montagem do Toyota Corolla.
Resultado:
Com esse projeto desafiador e inovador, a MRSUL entregou à Toyota uma solução que não apenas atendia às suas exigências de qualidade e eficiência, mas também demonstrava sua capacidade de desenvolver equipamentos personalizados para os mais complexos desafios industriais. A linha de montagem do Toyota Corolla experimentou um aumento significativo na eficiência operacional, redução de tempos de montagem e, consequentemente, aumento da produtividade, contribuindo para a satisfação do cliente e a excelência do produto final.